I've noticed that in much older posts I reported on costs of various types of insulations. More on this here. We have now finalized our cellulose insulation contract with Greensaver - a not-for-profit in the Toronto area. Costs for dense-packed cellulose insulation for walls seems to break down like this, at least on our project:
Walls: 4085 cubic feet, at 3.5lb/cf density = 14,300 lb cellulose, at 33 lb/bag, we need 433 bags at about $10ea. - so materials for the walls are $4330.
Attic: 4183cf at 2.0 lb/cf = about 8400 lb in the attic, or about $2550 worth of material.
Labour in the walls is about twice the material cost, and labour in the attic, about 70% of material costs.
Much thanks to Climatizer insulation of Toronto for providing a fantastic price on the material for our project! (They've had a tour of our house and took a step to support us as a contribution toward green initiatives). Here are the bags we will be using:
http://www.climatizerinsulation.com/CelluloseInsulation/Overview.aspx
In the past I've noted that spray-foams are about 10x the costs of cellulose and the other fibrous insulations. There is a bit more to note regarding this issue, which has some impacts on the 10x difference. I discovered this video on youtube: http://www.youtube.com/watch?v=F26eIesDDQg&feature=player_detailpage showing the use of pour foam - liquid foams that you pour into things. This is very similar or the same stuff that is used in the spray foam process, (it is basically the same, but additives may differ). The video points to Aeromarine Products http://aeromarineproducts.com, where you can purchase the foams right from the website. You'll notice you can purchase about 500 cubic feet of 2# foam for about $3900 - which works out to $7.80/cf, or about 10.8 cents/sf-R. This is still a lot more than cellulose, at $0.303/cf, or $0.0072/sf-R. Something like 15x the cost on the materials. Here is a place you can purchase spray-foam kits: http://www.sprayfoamkit.com/products/spray-foam-kits, and they also give you the prices right online - I love it when they do this. Here the price of spray foam on their largest kit works out to $14.3/cf - almost twice the price of the pour-foam. This is some 30x the cost of cellulose, R for R (not accounting for the fact that cellulose takes about twice the space to achieve the same R levels - the value of space and the construction details required to build this space for cellulose are pretty variable - but then, we are also not accounting for the health and environmental footprints of the two materials, which are vastly different as well, with cellulose miles ahead on both accounts). Note that labour costs are not included in the comparison, but given the labour portions noted above, we are still well ahead with cellulose.
Why is spray foam so much more expensive than the pour-foam? Pressure vessels, and possibly additives - but mostly the pressure vessel/ hoses, gun, etc. So the interesting point here is that if one must use urethane foam as a DIY, consider buying it in the liquid phase - that's what contractors do. If you don't need to spray it on walls, but can pour it into a cavity, this is really the way to go. In our case, we could have poured it into our walls - just like we will be 'pouring' the cellulose.
PS - We are purchasing larger amounts of mineral wool for our project as well, and Winroc has also given us excellent pricing on the material - again, to do their part to support 'green' projects. Our cost for this material worked out to about $0.034/sf-R - about 4.7 x the cost of cellulose, not accounting for installation labour, which would reduce the cost advantage of cellulose, probably bringing it nearly even with the Roxul.
Sunday, October 27, 2013
Tuesday, October 8, 2013
Above Floor Acoustic Assemblies, Basement Raised Floors, Porcelain Tile Exteriors
Damnation! A power outage caused the loss of almost the entire article I was writing for this post. Here it goes again.
Below are steel plates with screws holding the plywood floors in line with each other. We had issues with this (plywood not flush with adjacent plywood) due to the exposed beam ceiling below - we used good-one-side fir plywood for the sub-floor, and it does not come in T&G. With exposure to weather, the plywood warped and bowed. The plates, with short screws, bring it back in line. The steel was clear-coated. Not shown are holes we drilled just after this step to accept low voltage wiring for lights. In the background you will see the wood frame for a structural wall. One must be careful when framing a structural wall over an exposed beam ceiling - or any ceiling. Having the studs directly over joists is important to reduce warping of the plywood - but this is especially so in exposed beam ceilings. We also beefed up the bottom plates of the walls to support studs which were between joists - see photo. There is much to learn about open beam ceilings, in terms of construction finesse. Some concepts are thus:
On the right, we are laying in an above-floor acoustic treatment. Above the 3/4" ply subfloor, it consists of 6mm cork, then thick foamed poly sill gaskets under 1x4 sleepers. Sliced up roxul batts fill the spaces between sleepers. This allowed us to run our low voltage lighting wiring above the sub-floor as well (covered by Roxul in the photo), so no wiring is visible in the exposed beam ceiling below. Then we glued and screwed 3/4" T&G ply to the sleepers, again with short screws. The sleepers hold the ply together, and the ply holds the sleepers in place. Much cheaper than two layers of ply. Sound ratings unknown for this assembly, but the difference is very noticeable to our ears. This we are doing all over the 2nd floor except in washrooms and other areas of hydronic radiant flooring. Total thickness of this assembly not including the first sub-floor is just under 2". All the door openings were framed to accept this added height.
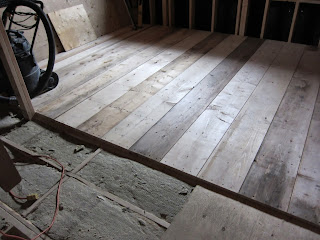
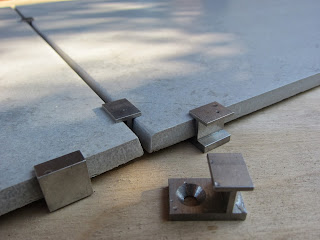
R-54 Insulation in the basement. That is an R32 Batt under the 2x6 joists in the basement floor, and an R22 roxul batt will fit between joists. Below these batts is a space made from PT lattice and landscape fabric, held up 2 to 3 inches using small PT blocks stapled to the batts. This lattice assembly keeps the insulation off the concrete floor beneath, and provides an unimpeded 'surface' drainage path for any water in the basement to flow towards the sump system. Any water which remains is able to dry through the insulation upwards. Any water in the insulation can also flow downwards through the porous landscape fabric. We were able to get the lattice material super cheap - it was culled material - an entire skidful for $50. The landscape fabric was about $8 for 150sf. We stapled it to the lattice.
In the next pic you see a 2x12 pine floor screwed to the joists in in the basement. We buried the screws about 1/8" so we could later sand the floor and get a somewhat finished surface. The boards will help to regulate moisture below the floor by passive moisture through them, but also by absorbing and releasing moisture. The main reason for using this kind of floor - low cost (again, we were able to purchase the material for a great deal - 25% discount from regular contractor pricing) at about $1.25/SF. This single layer of floor will become the finished floor (with sanding), so it means we can easily remove sections of flooring to inspect/service the spaces below in future. We therefore install without overlaps and plan the layout to allow removal. The floor feels extremely solid! Air sealing is not required at this floor - this was determined from previous air-tightness testing on the building, so we know we are already down to Passive House levels of air-tightness.
The last photo shows large porcelain tiles we plan to use in the cladding. These are 16x32" porcelain tiles. The clips you see are stainless steel. More on this later.
Below are steel plates with screws holding the plywood floors in line with each other. We had issues with this (plywood not flush with adjacent plywood) due to the exposed beam ceiling below - we used good-one-side fir plywood for the sub-floor, and it does not come in T&G. With exposure to weather, the plywood warped and bowed. The plates, with short screws, bring it back in line. The steel was clear-coated. Not shown are holes we drilled just after this step to accept low voltage wiring for lights. In the background you will see the wood frame for a structural wall. One must be careful when framing a structural wall over an exposed beam ceiling - or any ceiling. Having the studs directly over joists is important to reduce warping of the plywood - but this is especially so in exposed beam ceilings. We also beefed up the bottom plates of the walls to support studs which were between joists - see photo. There is much to learn about open beam ceilings, in terms of construction finesse. Some concepts are thus:
- Reduced height joists: Joists in the exposed beam area that are not as tall as the regular joists are advantageous. This is especially achievable if you have steel-beam joists, but heavy barn beams and other thick members would work as well. The reduced height allows one to add some thickness of structure above the exposed beams - such as diagonal planking, acoustic floors, and sleepers and wiring chases.
- Use all galvanized/stainless hardware to prevent stains due to weather exposure. Avoid making beams out of thinner, doubled members - It is difficult to double them properly due to the desire to avoid exposed fastenings. Also, protect the assembly from wetness after the floor above is built.
- Beware the structural wall above: Any wall built above exposed beams should have the studs aligned with the beams. Point loads due to door openings are to be avoided to reduce uneven loading on the exposed beams, which would cause some beams to deflect more than others, or even twist.
On the right, we are laying in an above-floor acoustic treatment. Above the 3/4" ply subfloor, it consists of 6mm cork, then thick foamed poly sill gaskets under 1x4 sleepers. Sliced up roxul batts fill the spaces between sleepers. This allowed us to run our low voltage lighting wiring above the sub-floor as well (covered by Roxul in the photo), so no wiring is visible in the exposed beam ceiling below. Then we glued and screwed 3/4" T&G ply to the sleepers, again with short screws. The sleepers hold the ply together, and the ply holds the sleepers in place. Much cheaper than two layers of ply. Sound ratings unknown for this assembly, but the difference is very noticeable to our ears. This we are doing all over the 2nd floor except in washrooms and other areas of hydronic radiant flooring. Total thickness of this assembly not including the first sub-floor is just under 2". All the door openings were framed to accept this added height.
R-54 Insulation in the basement. That is an R32 Batt under the 2x6 joists in the basement floor, and an R22 roxul batt will fit between joists. Below these batts is a space made from PT lattice and landscape fabric, held up 2 to 3 inches using small PT blocks stapled to the batts. This lattice assembly keeps the insulation off the concrete floor beneath, and provides an unimpeded 'surface' drainage path for any water in the basement to flow towards the sump system. Any water which remains is able to dry through the insulation upwards. Any water in the insulation can also flow downwards through the porous landscape fabric. We were able to get the lattice material super cheap - it was culled material - an entire skidful for $50. The landscape fabric was about $8 for 150sf. We stapled it to the lattice.
In the next pic you see a 2x12 pine floor screwed to the joists in in the basement. We buried the screws about 1/8" so we could later sand the floor and get a somewhat finished surface. The boards will help to regulate moisture below the floor by passive moisture through them, but also by absorbing and releasing moisture. The main reason for using this kind of floor - low cost (again, we were able to purchase the material for a great deal - 25% discount from regular contractor pricing) at about $1.25/SF. This single layer of floor will become the finished floor (with sanding), so it means we can easily remove sections of flooring to inspect/service the spaces below in future. We therefore install without overlaps and plan the layout to allow removal. The floor feels extremely solid! Air sealing is not required at this floor - this was determined from previous air-tightness testing on the building, so we know we are already down to Passive House levels of air-tightness.
The last photo shows large porcelain tiles we plan to use in the cladding. These are 16x32" porcelain tiles. The clips you see are stainless steel. More on this later.
Monday, October 7, 2013
Geo-Exchange is a Largely Untapped Resource in Canada
A new study found ground temperatures in Canada have risen significantly in recent years. Find this article here.
Jay Egg of Egg Geothermal in Florida writes in the Sept 2013 issue of Plumbing Engineer on some interesting approaches to ground coupling which were certainly new ideas to me. With geo-exchange (or 'groundsource'), we normally think of a flowing liquid in a closed loop of pipe inside the ground. This can be a regular pipe made of various materials, or it can be a completely sealed 'Heat Pipe' (look up heat pipes if you are not familiar with them http://en.wikipedia.org/wiki/Heat_pipe). However, there are other approaches of strong merit as well.
One such approach is the open-loop concept, in which one pumps water from the ground, harvests its thermal potential energy, and re-injects this water into the ground. This system has the significant advantage of reduced tendency for the local soil to drift in temperature, especially in dry periods.
Another approach is the standing column well (SCW). This I need to read more about.
Perhaps Here:
http://www.amazon.com/Modern-Geothermal-Engineering-Control-Applications/dp/0071792686/ref=sr_1_1?ie=UTF8&qid=1381195543&sr=8-1&keywords=modern+geothermalhttp://www.amazon.com/Modern-Geothermal-Engineering-Control-Applications/dp/0071792686/ref=sr_1_1?ie=UTF8&qid=1381195543&sr=8-1&keywords=modern+geothermal
A strong resource on ground temperatures in Canada:
http://archive.nrc-cnrc.gc.ca/eng/ibp/irc/cbd/building-digest-180.html
LT
Jay Egg of Egg Geothermal in Florida writes in the Sept 2013 issue of Plumbing Engineer on some interesting approaches to ground coupling which were certainly new ideas to me. With geo-exchange (or 'groundsource'), we normally think of a flowing liquid in a closed loop of pipe inside the ground. This can be a regular pipe made of various materials, or it can be a completely sealed 'Heat Pipe' (look up heat pipes if you are not familiar with them http://en.wikipedia.org/wiki/Heat_pipe). However, there are other approaches of strong merit as well.
One such approach is the open-loop concept, in which one pumps water from the ground, harvests its thermal potential energy, and re-injects this water into the ground. This system has the significant advantage of reduced tendency for the local soil to drift in temperature, especially in dry periods.
Another approach is the standing column well (SCW). This I need to read more about.
Perhaps Here:
http://www.amazon.com/Modern-Geothermal-Engineering-Control-Applications/dp/0071792686/ref=sr_1_1?ie=UTF8&qid=1381195543&sr=8-1&keywords=modern+geothermalhttp://www.amazon.com/Modern-Geothermal-Engineering-Control-Applications/dp/0071792686/ref=sr_1_1?ie=UTF8&qid=1381195543&sr=8-1&keywords=modern+geothermal
A strong resource on ground temperatures in Canada:
http://archive.nrc-cnrc.gc.ca/eng/ibp/irc/cbd/building-digest-180.html
LT
Subscribe to:
Posts (Atom)