There are a few options for waterproof exterior decks/balconies.
- Use roofing on the deck - for small areas, a single EPDM membrane - black or white - over a wood frame. I would think something needs to go on top of this to protect the membrane and make it more suitable to deck furniture and foot traffic - don't know what. Regular built-up roofing is not my preference - I've been on this kind of balcony before and found the odour quite strong - so I assume the tar and rubber are off-gassing - anyway, it makes the space unpleasant. I also would not do this over a deck which has had rigid insulation applied under the roofing membrane. There is a mushy feeling underfoot, and a sense of doubt as to whether one can place furniture on the surface.
- Extruded aluminum deck: These are generally powder coated extruded aluminum with either a rough or a smooth finish, such as available from Wahoo decks. These work well, I think, but they are pricey at about $19/SF. In our case, I couldn't find anyone local who imported them.
- Rubber membrane installed in a slanted scallop shape under the deck - it drains to one side - not an elegant solution, though cheap and simple. Perhaps more suited to decks over soil, to carry water away from the house.
- The option we chose: welded metal.
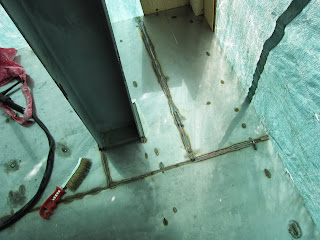 |
Welded stainless flashings not yet installed. |
Why? Cost of stainless is low right now - about $1.75/lb. (it was about $4.55/lb ten years ago). If you calculate the volume we are buying (1/8" thick plate is 18 cubic inches per sf), and multiply by the density of 0.3lb/cubic inch, you get the weight per sf. Multiplying by price, we get about $9.45/SF - not too costly for smaller areas and it's an easy purchase from local sources. I figured on a small area, I wanted to try this, and the thermal expansion issues would be minor - I expect this could be an issue on large expanses outdoors - the stainless steel has been in place a month or more now, and it is obvious that despite the high reflectivity, it does get quite warm in the hot sun - like a roof, so thermal expansion is something to keep in mind, as they do on steel roofs. Stainless steel will also accept tons of abuse without any maintenance, feels solid underfoot, doesn't smell bad, and modifications can be made by welding to it....
I always wondered why people don't employ this solution in their projects for roofs and balcony floors, but even for interior floors. What I found was that it was a fair bit of work, but not ridiculous, and the result is (I'm hoping) going to prove very practical and durable. The steel frame in grey primer you see in the photos is regular structural steel, 3" deep C-channels welded to 6" deep hollow beams. It is far stronger than it needs to be, but we ended up doubling up the joists from what is in the photos - It is a slightly difficult calculation to figure out the floor deflection as a diaphragm, and my rough numbers turned out to be close enough, but I didn't trust them, figuring the floor was supported on all sides. The deflection of the diaphragm proved noticeable enough and it was simple to add additional joists so they ended up at 9" on centre, originally about 18" OC. The floor feels very rigid now. Originally, I thought I would have it plug welded from above and ground smooth, but the mag drill wouldn't stick well enough to the steel through the 1/8" stainless, so we mig-welded from below. We tig-welded the seams from above (with some mig tacking from below) as the photos show - this is the reason for the tarp.
One thing I really like about stainless - I always feel it is easy to add to it with welding. You needn't grind off the paint as you would have to with steel, and then re-paint after welding. I knew I'd want to add some fittings, possibly cleats, hold-downs, etc. This is easily done on exposed stainless. The flashings were all welded on. Most are 22ga, bent on site with a heavy brake - this proved tricky to weld to the 1/8" plate. The flashing under the door was 14ga, fitted into a grove in the PVC door frame - it is just a window placed on the floor.
Distortion: There was some distortion. We had a 1/4"/ft (1 in 50) slope on the floor. In some areas there was enough distortion to upset this slope and cause pooling - mainly on the long seam you can see near the 6" deep beam, where small sections were welded on. I'm not too concerned, but we'll be working to correct this and see where it goes.
We used 304L for all the stainless - I'd done a little stainless tig-welding before, and I was familiar with the significant movement of carbon and chromium within the material in the heat-affected zone. This causes non-stainless areas to appear near the weld afterwards - this is why you need to passivate the stainless after welding (dip into an acid bath to remove the surface areas of non-stainless material). In our case we would not be giving acid baths to the stainless. The 'L' in the material designation stands for 'Low carbon', which reduced post-weld corrosion quite a lot. As it turned out, we did have some surface corrosion appearing on our project, but it was not due to the welds, which seemed to work well. It was actually due to the use of wire-brushing with steel brushes. We switched to stainless brushing after noticing this and all was well.
Welding was with both 308 and 309 rod - yes, welding regular steel to stainless is entirely fine and routinely done.
The reflection off the stainless is very bright - it is blinding, actually. I was hoping this would be a good thing to raise the light incident on the deeply inset glass balcony door - but we did plan to have real wood-slat tiles or boards to block this reflection anyways. I also plan to do some solar experiments on this balcony, so the reflective surface may be an interesting feature for this. I've not seen anything on how to integrate this effect into the Passive House thermal modelling. There are solar reflectors you can purchase that actually track the sun, and reflect it into a given window on the house, such as these:
http://www.creativemachines.com/special_projects/Solar_Mirror/Solar_Mirror.html
http://www.egis-rotor.de/helio_us.html This would be a significant energetic effect on the house - one that might be an attractive solution in some cases. This one is really cute:
http://wikoda.com/.
However, if this were part of a design, I would place the reflection-receiving windows high on the wall of the house reduce glare inside the building.
The experience with this has had me consider other metal flooring solutions: A carbon steel sub-floor/finished floor in the basement (the beauty of this is that the subfloor is the finished floor, reducing labour and materials, and the floor plates - I'd use 4'x2' plates, screwed down - can be removed to gain access to the space beneath)......and also radiant stainless steel staircases (designed well, a radiant staircase can be good for both cooling and heating, since the stair is both a floor and a ceiling).
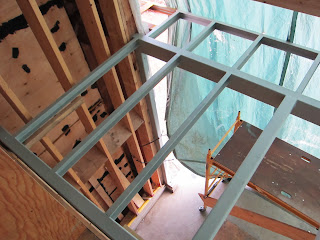 |
C3x5 (75mm deep, 7.5kg/m) C-channels welded to 3"x6" deep hollow steel tube beam - Beam wall was 3/16" or 1/4" thick. |
 |
Too bad we've not cleaned off the dark residues from the welding for the photo. Need more photos of this part of the project. |