Robert Riversong's description of a fine set of his own house contruction techniques. These are particularly green and very interesting - Modified Larsen trusses ('Riversong Truss'), raw green lumber, no plywood, dense pack cellulose, and no poly vapour barrier. Turns a few ideas upside down - a refreshing read.
http://www.builditsolar.com/Projects/SolarHomes/LarsenTruss/LarsenTruss.htm
http://www.builditsolar.com/Projects/SolarHomes/LarsenTruss/History.htm
Wednesday, December 29, 2010
Saturday, December 11, 2010
More Passive House Basement, Wall and Roof Details
I thought I would post an earlier design I had prepared. We almost went for permit with this, but as we have a little more time now, I'm working to reduce the cost and foam contents of the foundation details, as you'll see in the earlier Dec 9 blog. There is also a little issue with the wall and roof structures - The amount of TJI's used. They are nice as one can get them easily in long continuous lengths, but the pricing has been an issue - I found them quite expensive compared to solid dimensional lumber. The other drawback is that they have very little tensile strength in the lateral direction - ie the flanges can pull off - they were never designed to take loading in that direction. My concern is that in the wall assy, they might not be great if the wall finish was heavy. In the roof, uplift forces may be a concern. Larsen trusses apparently can take a little more in this regard - but I think some testing should be done.
Thursday, December 9, 2010
Passive House Basement Foundation Detail
Here is a basement foundation section I came up with recently. I'm excited about this configuration for three reasons:
1. It uses very little rigid foam, which constitutes a cost saving, good environmental stewardship, and leads to good indoor air quality. the rigid foam may even be able to be eliminated altogether, depending on the thermal analysis.
2. The construction process will prove fairly straightforward and simple, with walls generally being able to be built in the flat and tilted up. The slab is the only concrete in the system, which also keeps the environmental footprint down. It is easy to build. The elevator pit can be incorporated into the wooden floor system, rather than needing to be formed into the concrete.
3. The exterior wall can be made with concrete, if a client is really too nervous about the wood, though the insulation value is reduced.
Other features, both good and bad, of this design include:
1. It uses very little rigid foam, which constitutes a cost saving, good environmental stewardship, and leads to good indoor air quality. the rigid foam may even be able to be eliminated altogether, depending on the thermal analysis.
2. The construction process will prove fairly straightforward and simple, with walls generally being able to be built in the flat and tilted up. The slab is the only concrete in the system, which also keeps the environmental footprint down. It is easy to build. The elevator pit can be incorporated into the wooden floor system, rather than needing to be formed into the concrete.
3. The exterior wall can be made with concrete, if a client is really too nervous about the wood, though the insulation value is reduced.
Other features, both good and bad, of this design include:
- Simplified plumbing, since most of it can be done above the slab.
- Possible issues with finished space - the building department may see the basement as finished space and charge more for the permit and subsequent property taxes.
- Pressure treated lumber - You'll see that the exterior shell suggests a very thin shield against the soil - I'm thinking 5/16" fiber cement siding, with asphaltic damproofing, then the HDPE dimpled membrane. This does away with the poured concrete wall - which takes a lot of space - say 8 or 10inches, which is a major financial and enviro cost, and gives nothing to insulation - and proposes instead a very thin shell, held up with lumber. The fiber cement shell is provided with the above moisture protection, but also with an additional drainage layer behind. This can prove an effective measure to ventilate the thick, insulated basement foundation wall, as well as to keep that outer shell very dry. The question, after all this, is - do we use PT lumber on the outer frame, or regular lumber? We all know the PT lumber is very hard on the environment - so my preference is to do away with it. Use regular lumber. The battens to which the FC siding is attached can be plastic-wood. - I'm still trying to figure that out - but the issue with all this is the buliding department - will they accept this untreated-lumber below grade construction? This will be a very interesting issue.
Here is the scan of my sketch:
Wednesday, December 8, 2010
Two Zoning Bylaws at Once - Illegal?
I was informed by Brian Parker (urban planner in Toronto) that section 34(30) of the planning act states the new bylaw mustn't be enforced by the OMB until all appeals have been dealt with.
Here are relevant excerpts from the planning act, R.S.O. 1990, Chapter P.13, Section 34:
-------------------------------------------------------------------------------------------------------------
Appeal to O.M.B.
To me this means the bylaw is deemed to have come into force on the day it was passed, but shall not be enforced until all appeals have been disposed. This is an interesting situation. Lets take some test scenarios:
Here are relevant excerpts from the planning act, R.S.O. 1990, Chapter P.13, Section 34:
-------------------------------------------------------------------------------------------------------------
Appeal to O.M.B.
(19) Not later than 20 days after the day that the giving of notice as required by subsection (18) is completed, any of the following may appeal to the Municipal Board by filing with the clerk of the municipality a notice of appeal setting out the objection to the by-law and the reasons in support of the objection, accompanied by the fee prescribed under the Ontario Municipal Board Act:
1. The applicant.
2. A person or public body who, before the by-law was passed, made oral submissions at a public meeting or written submissions to the council.
3. The Minister. 2006, c. 23, s. 15 (10).
When by-law deemed to have come into force
(21) When no notice of appeal is filed under subsection (19), the by-law shall be deemed to have come into force on the day it was passed except that where the by-law is passed under circumstances mentioned in subsection 24 (2) the by-law shall not be deemed to have come into force on the day it was passed until the amendment to the official plan comes into effect. R.S.O. 1990, c. P.13, s. 34 (21); 1994, c. 23, s. 21 (10); 1996, c. 4, s. 20 (8).
Hearing and notice thereof
(24) On an appeal to the Municipal Board, the Board shall hold a hearing of which notice shall be given to such persons or bodies and in such manner as the Board may determine. R.S.O. 1990, c. P.13, s. 34 (24).
Restriction re adding parties
(24.1) Despite subsection (24), in the case of an appeal under subsection (11) that relates to all or part of an application for an amendment to a by-law that is refused, or in the case of an appeal under subsection (19), only the following may be added as parties:
1. A person or public body who satisfies one of the conditions set out in subsection (24.2).
2. The Minister. 2006, c. 23, s. 15 (12).
Same
(24.2) The conditions mentioned in paragraph 1 of subsection (24.1) are:
1. Before the by-law was passed, the person or public body made oral submissions at a public meeting or written submissions to the council.
2. The Municipal Board is of the opinion that there are reasonable grounds to add the person or public body as a party. 2006, c. 23, s. 15 (12).
New information and material at hearing
(24.3) This subsection applies if information and material that is presented at the hearing of an appeal described in subsection (24.1) was not provided to the municipality before the council made the decision that is the subject of the appeal. 2006, c. 23, s. 15 (12).
Same
(24.4) When subsection (24.3) applies, the Municipal Board may, on its own initiative or on a motion by the municipality or any party, consider whether the information and material could have materially affected the council’s decision, and if the Board determines that it could have done so, it shall not be admitted into evidence until subsection (24.5) has been complied with and the prescribed time period has elapsed. 2006, c. 23, s. 15 (12).
Notice to council
(24.5) The Municipal Board shall notify the council that it is being given an opportunity to,
(a) reconsider its decision in light of the information and material; and
(b) make a written recommendation to the Board. 2006, c. 23, s. 15 (12).
Council’s recommendation
(24.6) The Municipal Board shall have regard to the council’s recommendation if it is received within the time period mentioned in subsection (24.4), and may but is not required to do so if it is received afterwards. 2006, c. 23, s. 15 (12).
Conflict with SPPA
(24.7) Subsections (24.1) to (24.6) apply despite the Statutory Powers Procedure Act. 2006, c. 23, s. 15 (12).
Coming into force
(30) If one or more appeals have been filed under subsection (19), the by-law does not come into force until all of such appeals have been withdrawn or finally disposed of, whereupon the by-law, except for those parts of it repealed or amended under subsection (26) or as are repealed or amended by the Lieutenant Governor in Council under subsection (29.1), shall be deemed to have come into force on the day it was passed. 1996, c. 4, s. 20 (13); 2004, c. 18, s. 6 (4).
-------------------------------------------------------------------------------------------------------------To me this means the bylaw is deemed to have come into force on the day it was passed, but shall not be enforced until all appeals have been disposed. This is an interesting situation. Lets take some test scenarios:
- The appeals are going forward. The bylaw is not enforced. The appeals, a year later, are all withdrawn or come to no result. The bylaw is then deemed to have come into force on the day it was passed, now a year ago. What happens to all those files that were processed without the bylaw enforced?
- The appeals are going forward. The bylaw is enforced, contrary to the planning act. All appeals come to no result. The bylaw is comes into force on the day it was passed, now a year ago. Everything is fine, except the law was broken for a year, with a bunch of people suffering the consequences. Now all those people can turn around and sue.
- The appeals are going forward. The bylaw is not enforced. They result in changes to the bylaw. A new bylaw is drafted and is subsequently passed, a year later. No legal battle arises for the files process through-out that year.
- The appeals are going forward. The bylaw is illegally enforced. The appeals process results in changes to the bylaw. A new bylaw is passed or amendments are passed. All those people who suffered the enforcement in the interrum can sue the city?
Perhaps a useful concept in resolving this could be to recognize the planning act is making a distinction between the date of enactment and the date of enforcement. It seems to imply enforcement does not automatically follow upon enactment of a zoning bylaw, but the date of enactment can be placed in the past, upon resolution of appeals.
......
Toronto Enforcing Two Zoning Bylaws Simultaneously
Oh the Pain! The Horror!
City of Toronto is enforcing both the old and new zoning bylaws simultaneously. I contacted Joe D'Abramo (Acting Director - Zoning?) last night and he returned my phone call this morning (bless him). He confirmed that yes, the two zoning bylaws are in effect simultaneously, and this will go on for some time, until all the appeals have finally been dealt with - so this means for a year or more - (I am thinking more - this is a costly and big process). There are 694 appeals. - Apparently 90% of them are lot/site specific.
Presently Joe's group are analyzing and sorting through the appeals. They hope to provide direction (early in the new year, he said) on which parts of the new bylaw are not under contest, so that the OMB can work to complete the instating of the bylaw on those parts only.
Below are a couple of links I came across on the zoning bylaw - neither discuss the enforcement of two bylaws, but the first gives a pretty good summary of contents and old-to-new differences, and the second discusses the appeals slightly.
http://www.gowlings.com/knowledgecentre/enewsletters/realestate/htmfiles/V1N02_20100920a.en.html
http://www.nationalpost.com/todays-paper/Harmonized+zoning+bylaw+spurs+appeals/3859605/story.html
Note --- see the later posts to get analysis and legality of this double-enforcement approach------
Joe explained that the new bylaw will be in effect retroactively to the August 25th, 2010 date, when the bylaw is finally cleared - but this bodes darkly for current projects - buildings will be designed based on both bylaws, and they will already be built or well underway by the time the new zoning bylaw is fully implemented - meanwhile the appeals process will change the bylaw - which means any buildings being permitted in the interrum will likely not conform regardless - or if they did, it would be because they paid $1700 for the committee of adjustment review and waited over 4 months for the result, and based on a law that is changing! This seems unfair to all those people who are in the building process right now.
On the whole, I just find it unreasonable to both building departments and related services and builders that the new bylaw cannot go through it's birthing woes BEFORE it becomes enforced - the need to enforce it retroactively seems innappropriate, to put it mildly.
City of Toronto is enforcing both the old and new zoning bylaws simultaneously. I contacted Joe D'Abramo (Acting Director - Zoning?) last night and he returned my phone call this morning (bless him). He confirmed that yes, the two zoning bylaws are in effect simultaneously, and this will go on for some time, until all the appeals have finally been dealt with - so this means for a year or more - (I am thinking more - this is a costly and big process). There are 694 appeals. - Apparently 90% of them are lot/site specific.
Presently Joe's group are analyzing and sorting through the appeals. They hope to provide direction (early in the new year, he said) on which parts of the new bylaw are not under contest, so that the OMB can work to complete the instating of the bylaw on those parts only.
Below are a couple of links I came across on the zoning bylaw - neither discuss the enforcement of two bylaws, but the first gives a pretty good summary of contents and old-to-new differences, and the second discusses the appeals slightly.
http://www.gowlings.com/knowledgecentre/enewsletters/realestate/htmfiles/V1N02_20100920a.en.html
http://www.nationalpost.com/todays-paper/Harmonized+zoning+bylaw+spurs+appeals/3859605/story.html
Note --- see the later posts to get analysis and legality of this double-enforcement approach------
Joe explained that the new bylaw will be in effect retroactively to the August 25th, 2010 date, when the bylaw is finally cleared - but this bodes darkly for current projects - buildings will be designed based on both bylaws, and they will already be built or well underway by the time the new zoning bylaw is fully implemented - meanwhile the appeals process will change the bylaw - which means any buildings being permitted in the interrum will likely not conform regardless - or if they did, it would be because they paid $1700 for the committee of adjustment review and waited over 4 months for the result, and based on a law that is changing! This seems unfair to all those people who are in the building process right now.
On the whole, I just find it unreasonable to both building departments and related services and builders that the new bylaw cannot go through it's birthing woes BEFORE it becomes enforced - the need to enforce it retroactively seems innappropriate, to put it mildly.
Thursday, October 14, 2010
Hot Dip Galvanizing - Costs, etc.
OK, this topic is not really on Passive House.
Hot Dip Galvanizing in Toronto:
Cost: Rough Ballpark is $.40/lb of finished galvanised item, $295 min charge
Spec: ASTM A123, min thickness 3.4mil or 610g/Sqm or 2oz/SF
Tubular sections will require holes about 30% of section width each end of frame/item.
Bath is at 840deg F, so no sealed sections will be allowed due to danger of exploding, though part can also float in the molten zinc bath.
Partial dipping is possible but there can be practical issues with the conveying machinery and part set-up - so it depends on what the part looks like - shape, etc.
I love finding out stuff like this.
LT
Hot Dip Galvanizing in Toronto:
Cost: Rough Ballpark is $.40/lb of finished galvanised item, $295 min charge
Spec: ASTM A123, min thickness 3.4mil or 610g/Sqm or 2oz/SF
Tubular sections will require holes about 30% of section width each end of frame/item.
Bath is at 840deg F, so no sealed sections will be allowed due to danger of exploding, though part can also float in the molten zinc bath.
Partial dipping is possible but there can be practical issues with the conveying machinery and part set-up - so it depends on what the part looks like - shape, etc.
I love finding out stuff like this.
LT
Tuesday, September 28, 2010
New Zoning Bylaw was passed in Toronto!
Note ------ see later blog posts in December for analysis of the double-enforcement of new and old bylaws simultaneously. ---------
Oh Boy,
So much has happenned since the last blog entry.
We finished our structural engineering and we've completed the drawings....at least to get them ready for permit. However, the zoning bylaw in Toronto has changed to a new one, Bylaw 1156-2010, passed by City Council Aug 27th. Apparently the idea was to harmonize. The wonderful thing is that the new bylaw is all online, so its no longer a secret, like it was before - you had to go to the library to get it, and that was only a part of it.
The big thing for us is that that the building height limitation has changed from 8.8m to the mid-point of the roof to 10m to the peak. - Our building is about 45inches too tall!
This seemed a major problem to to us, and we re-geared our plans and figured we'd go for a zoning adjustment, and then start construction in the spring.
However, we had more contact with the city now as we prepared our plans for the adjsutment application (which the city says will take 3 to 4 months minimum), and today the city called us to discuss our 2nd set of plans (the first was in May or June). Well, the news is that the new zoning bylaw is being appealed, so the city has to double-review all files-in-process to ensure they comply with BOTH old and new zoning bylaws! - this is Crazy!
We get all the restrictions of the new and old bylaws, and the benefits of one are often degraded or cancelled by the other. - For example:
Comparing old zoning R4 to new zoning R:
Apply for a zoning adjustment for every feature that meets one but not the other - perhaps in the process we can get the best of both?
Oh Boy,
So much has happenned since the last blog entry.
We finished our structural engineering and we've completed the drawings....at least to get them ready for permit. However, the zoning bylaw in Toronto has changed to a new one, Bylaw 1156-2010, passed by City Council Aug 27th. Apparently the idea was to harmonize. The wonderful thing is that the new bylaw is all online, so its no longer a secret, like it was before - you had to go to the library to get it, and that was only a part of it.
The big thing for us is that that the building height limitation has changed from 8.8m to the mid-point of the roof to 10m to the peak. - Our building is about 45inches too tall!
This seemed a major problem to to us, and we re-geared our plans and figured we'd go for a zoning adjustment, and then start construction in the spring.
However, we had more contact with the city now as we prepared our plans for the adjsutment application (which the city says will take 3 to 4 months minimum), and today the city called us to discuss our 2nd set of plans (the first was in May or June). Well, the news is that the new zoning bylaw is being appealed, so the city has to double-review all files-in-process to ensure they comply with BOTH old and new zoning bylaws! - this is Crazy!
We get all the restrictions of the new and old bylaws, and the benefits of one are often degraded or cancelled by the other. - For example:
Comparing old zoning R4 to new zoning R:
- Height limitations are screwed up - in old, there are two limits based on whether the roof is flat or sloped, being 8.0m and 8.8m (to midpoint of roof) respectively. Now in the new, the limit is 10mregardless, except 2 opposing principal walls must be less than 7m. So what if the building is 10m, with a flat section at the top, but meets the wall heights requirement?
- Old zoning stipulates 2 stories max. New code doesn't care - so what if the building has 3 stories?
- Old bylaw does not allow roofs over porches which are exempt from coverage - only canopies. New bylaw does - so what do you do if you want the roof?
- Old zoning provides for 0.5m roof overhangs without coverage penalty. New zoning allows for 0.9m. What to put into the design?
Apply for a zoning adjustment for every feature that meets one but not the other - perhaps in the process we can get the best of both?
Wednesday, August 18, 2010
Absorption Chillers, Einstein refridgerators and cool stuff like that
Check out this Youtube TED video on a low-cost, high-tech refridgeration technology by Adam Grosser;
http://www.youtube.com/watch?v=HSdXqmnNCp0
Crazy cool stuff - use a campfire as an energy source for cooling 3 gallons of water down to just above 0deg C, for 24hrs, in a 30deg C environment. Funny thing is that to figure out this technology, they had to get the entire thermodynamics dept at Stanford involved and used CFD (computational fluid dynamics) to regenerate the property tables for ammonia, discovering that the old ones were all wrong.....this is pretty freaky stuff.
So, we need something that takes energy from the sun to power an absorption chiller designed to cool down a house.
Alternative: Take the heat from inside the house (via the ERV/HRV), concentrate it to use as a heat source to power the absorption chiller to cool the house (again via ERV/HRV). Any losses in efficiencies (waste heat) go to the domestic hot water system. How cool would that be?
The Einstein refridgerator (an absorption chiller variant) uses no moving parts. A guy named M. McCulloch is involved with reviving this technology at Oxford university.
Now the search for practical units in the marketplace begins.
LT
http://www.youtube.com/watch?v=HSdXqmnNCp0
Crazy cool stuff - use a campfire as an energy source for cooling 3 gallons of water down to just above 0deg C, for 24hrs, in a 30deg C environment. Funny thing is that to figure out this technology, they had to get the entire thermodynamics dept at Stanford involved and used CFD (computational fluid dynamics) to regenerate the property tables for ammonia, discovering that the old ones were all wrong.....this is pretty freaky stuff.
So, we need something that takes energy from the sun to power an absorption chiller designed to cool down a house.
Alternative: Take the heat from inside the house (via the ERV/HRV), concentrate it to use as a heat source to power the absorption chiller to cool the house (again via ERV/HRV). Any losses in efficiencies (waste heat) go to the domestic hot water system. How cool would that be?
The Einstein refridgerator (an absorption chiller variant) uses no moving parts. A guy named M. McCulloch is involved with reviving this technology at Oxford university.
Now the search for practical units in the marketplace begins.
LT
Friday, August 13, 2010
Hot Water and Heating with Heat pumps
Using only electricity for DHW and heat on our project results in a primary energy consumption of some 180kWh/m^2an, so this simplest of solutions is definitely not passive house. Using heat pumps exclusively for both cuts the number in half (the limit is 120kWh...).
There are many types of heat pump module available. Therma-Vent, Aqua-Plus, Heat Harvester, HotPlate... The issue is heat pumps degrade in COP significantly as the output temperatures reach 55 to 60deg C for DHW (but they can still do this with a COP of about 2).
Anyway, we need to look at harvesting the incoming ventilation air heat in summer and the outgoing ventilation air heat in summer, and the outgoing ventilation air heat in winter - got that?
The other thing is to integrate this all with solar thermal, and a 600' 3/4" pex loop in the ground should provide a fair bit of the needed energy as well. It would be nice to have an insulated concrete tank where we can dump excess heat in summer and recover it in winter. The earthtube seems more and more of an impracticality, though it is still a minor possibility.
LT
There are many types of heat pump module available. Therma-Vent, Aqua-Plus, Heat Harvester, HotPlate... The issue is heat pumps degrade in COP significantly as the output temperatures reach 55 to 60deg C for DHW (but they can still do this with a COP of about 2).
Anyway, we need to look at harvesting the incoming ventilation air heat in summer and the outgoing ventilation air heat in summer, and the outgoing ventilation air heat in winter - got that?
The other thing is to integrate this all with solar thermal, and a 600' 3/4" pex loop in the ground should provide a fair bit of the needed energy as well. It would be nice to have an insulated concrete tank where we can dump excess heat in summer and recover it in winter. The earthtube seems more and more of an impracticality, though it is still a minor possibility.
LT
Windows again
Had another conversation with Thermotech. They confirmed the use of the zeros (apparently PHIUS is in agreement with this) in the PHPP for Psi spacer and Psi installation. This makes a huge difference to the energy calculations reducing specific annual energy by a kWh/m^2 or more.
Also the cost of their windows with the 322Gain+ triple pane glass is about $65-70/SF depending on options. The windows come with or without installation flanges, with or without brick mold.
No tilt and slide patio doors available - so this is an issue, since I don't want to pay shipping from europe for just a couple of doors.
LT
Also the cost of their windows with the 322Gain+ triple pane glass is about $65-70/SF depending on options. The windows come with or without installation flanges, with or without brick mold.
No tilt and slide patio doors available - so this is an issue, since I don't want to pay shipping from europe for just a couple of doors.
LT
Wednesday, August 4, 2010
Windows - Thermotech vs Others in PHPP
I went through detailed modelling of the thermal envelope recently and compared Thermotech windows to Euro-style PH windows:
Here's an email I sent to Stephen Thwaites of Thermotech about the results:
Dear Stephen and Ken,
.......preamble....
Our design is a 2.5 storey house 41.5ft e-w by 36.5ft n-s. It is a rectangualr box with a gable roof, the ends facing e-w. Very simple and compact shape, with basement. 35 Openings totalling 39.9Sq m of windows, including 4 doors with 1/2 lites and including door and window frames, 20.9 sqm of that on the south.
What I found is:
1. Compared Thermotech glass to a high-performance 'Low-E 0.51 Neutralite Guardian Luxguard (item 35 in the PHPP)' glass with SHGC 0.51 and Ug 0.51, the model showed a 1kWh/m^2an advantage over the Thermotech 322Gain+(75/68) glass. With Thermotech glass, we were at 12.966kWh, and with the Neuatrilite, it was down to 11.99. This compares to the 15kWh/m^2an threshold to be a passive house. The comparison was done with the Thermotech casement frames in the model.
2. Returning the model to the Thermotech glass, I compared Thermotech frames to Optiwin Solarfassade frames, but keeping the 4 doors as before, which are generic. The narrowness of the Thermotech frames (0.68m compared to Optiwin's 0.100) is definitely a significant boost to performance. Switching from Thermotech Casements all around to the Optiwin degraded the building's performance from 12.97kWh/m^2an to 14.81 - a very significant difference. Fixed (non opening) Thermotech windows will be good as well, of course, though there is still more comparing to do.
I didn't look at the sliding glass doors since I don't think they'll meet airtightness needs without the lift and slide hardware.
LT
Here's an email I sent to Stephen Thwaites of Thermotech about the results:
Dear Stephen and Ken,
.......preamble....
Our design is a 2.5 storey house 41.5ft e-w by 36.5ft n-s. It is a rectangualr box with a gable roof, the ends facing e-w. Very simple and compact shape, with basement. 35 Openings totalling 39.9Sq m of windows, including 4 doors with 1/2 lites and including door and window frames, 20.9 sqm of that on the south.
What I found is:
1. Compared Thermotech glass to a high-performance 'Low-E 0.51 Neutralite Guardian Luxguard (item 35 in the PHPP)' glass with SHGC 0.51 and Ug 0.51, the model showed a 1kWh/m^2an advantage over the Thermotech 322Gain+(75/68) glass. With Thermotech glass, we were at 12.966kWh, and with the Neuatrilite, it was down to 11.99. This compares to the 15kWh/m^2an threshold to be a passive house. The comparison was done with the Thermotech casement frames in the model.
2. Returning the model to the Thermotech glass, I compared Thermotech frames to Optiwin Solarfassade frames, but keeping the 4 doors as before, which are generic. The narrowness of the Thermotech frames (0.68m compared to Optiwin's 0.100) is definitely a significant boost to performance. Switching from Thermotech Casements all around to the Optiwin degraded the building's performance from 12.97kWh/m^2an to 14.81 - a very significant difference. Fixed (non opening) Thermotech windows will be good as well, of course, though there is still more comparing to do.
I didn't look at the sliding glass doors since I don't think they'll meet airtightness needs without the lift and slide hardware.
LT
Thursday, July 29, 2010
SIPS for an R100 Roof
Well, the roof is not turning out to be easy. the first option I've been working on is a 2x6 rafter system conventionally framed with sheathing and Grace Ice and Water Shield on the outside of it as an air and vapour barrier. (PERSIST system). Then 20" deep I-joists go on top of that assy, sitting on 2x4 purlins on the flat to minmimize thermal bridging. Something is done at the top to form a 2.5" deep vent channel and then another layer of sheathing and then the roofing. Long process, some big parts of it on scaffolding. Costs are significant too. Costing is complicated, but I have most of the numbers. It is something like $19,000 of materials not including roofing. Labour - who knows?
Then the SIPS solution. the idea would be to frame the roof with the previously planned 2x6 rafters, then place the SIPS on top. Air and vapour barriers are not needed, and neither is the vent channel. It is solid insulation right through to the outside. If code officials balk, then a conventional poly VB can be placed on the inside of hte inner frames.
Talked with Kent Truss in Barrie - they say the value of the SIPS materials for this application is about $30,000 delivered to site, (SIPS and their accessories only - no roofing). The roof is a simple 8/12 pitch gable, total 2160SF on the outside. Apparently this is about 2 truckloads of SIPS materials.
Installation is an additional $2/sf approx, but in our case, maybe double that. Sips are max 12.25" thick - this is for manufacturing reasons, and also the 2x12 studs used to connect them. since the thickest SIPs are R45.5, they would need to use 2 layers, the second being faced one-side only with OSB. Special 14" long screws are used to secure the SIPS. OSB facings are 7/16" standard thickness.
Also, largest SIPS panels available from Insulspan are 8'x24' (x previously mentioned 12.25"thk).
LT
Then the SIPS solution. the idea would be to frame the roof with the previously planned 2x6 rafters, then place the SIPS on top. Air and vapour barriers are not needed, and neither is the vent channel. It is solid insulation right through to the outside. If code officials balk, then a conventional poly VB can be placed on the inside of hte inner frames.
Talked with Kent Truss in Barrie - they say the value of the SIPS materials for this application is about $30,000 delivered to site, (SIPS and their accessories only - no roofing). The roof is a simple 8/12 pitch gable, total 2160SF on the outside. Apparently this is about 2 truckloads of SIPS materials.
Installation is an additional $2/sf approx, but in our case, maybe double that. Sips are max 12.25" thick - this is for manufacturing reasons, and also the 2x12 studs used to connect them. since the thickest SIPs are R45.5, they would need to use 2 layers, the second being faced one-side only with OSB. Special 14" long screws are used to secure the SIPS. OSB facings are 7/16" standard thickness.
Also, largest SIPS panels available from Insulspan are 8'x24' (x previously mentioned 12.25"thk).
LT
Tuesday, July 27, 2010
Windows Again
Wow,
There are some fantastic window discussions out there. Green Building Advisor has so much information in it. Fantastic!
Here is the link (Thanks to the Loading Dock Blog for the link http://blog.loadingdock5.com/?p=192 )
http://www.greenbuildingadvisor.com/blogs/dept/musings/passivhaus-windows
There are some fantastic window discussions out there. Green Building Advisor has so much information in it. Fantastic!
Here is the link (Thanks to the Loading Dock Blog for the link http://blog.loadingdock5.com/?p=192 )
http://www.greenbuildingadvisor.com/blogs/dept/musings/passivhaus-windows
Window Sourcing
Gualhofer, Optiwin, are two Euro window makers selling in NA.
Here is the Gaulhofer NA site: http://www.gaulhoferwindows.com/contact-us.php
Optiwin NA is easy to find.
Their Frostkorken door is approx $2000, I think, with VIP panels inside, rated R60 (!), this price with no frills.
Here is the Gaulhofer NA site: http://www.gaulhoferwindows.com/contact-us.php
Optiwin NA is easy to find.
Their Frostkorken door is approx $2000, I think, with VIP panels inside, rated R60 (!), this price with no frills.
Windows and really good Windows!
Conversation with Stephen at Thermotech was very enlightening. Here is some info about their windows and windows in general.
Only 3 NA companies make the high-performance windows needed for Passive House.
Here are some numbers on sizing:
Only 3 NA companies make the high-performance windows needed for Passive House.
- Serious Windows
- Thermotech
- Fibertec
Here are some numbers on sizing:
- Tilt and turn windows work best at about 3 to 4ft wide.
- Triple pane casements should not be wider than 34" or the hinge hardware becomes inadequate
- Casement dimensions are max about 34"x72".
- Awning windows are good up to 4'x4' sizes.
- Pricing is by perimeter, except the customer base prefers 'united length'. At a certain size, windows jump in price due to the need to thicken the glass, which is determined by wind pressures and CSA codes. This size is 95 united inches (outside dim of windows, length plus width). Above 95 Ui, glass must be 4mm thick, rather the 3.
- Thermotech recently began offering a triple pane glass with low -e, argon, and now low-iron glass called their 322 Gain Plus. The low iron improves SHGC, though drops R value slightly. Krypton fill adds about $20 to $30 per SF to window costs (!).
- Nice window hardware is by Roto, Segania, G. U.
- Energy Rating (ER) rating is a Canadian rating system for windows that takes solar heat gains into account as well as R-value. Thermotech windows perform very well in this rating system, in which solar gains over 200 days in the year are averaged.
- Here is a window discussion in GreenBuildingAdvisory.com: http://www.greenbuildingadvisor.com/community/forum/energy-efficiency-and-durability/14850/serious-windows-vs-thermotech-fibertec-inline
Wednesday, July 21, 2010
Footing Insulations
Structural connections are the hardest parts to design for thermal bridge-free construction. I've decided to install insulation under my strip footings. There are high-strength insulation products such as Foamglas and Pur-knit and others. They are expensive, and Foamglas is friable (brittle). Therefore I plan to use HI-load 60. An XPS 60-psi compressive strength rated insulation under the strip footings. This stuff is R-5 per inch. For nearly twice the price, you can buy HI-load 100, and Foamglass is beyond that price. As an added benefit, the HI-60 comes in thickness up to 3".
The DOW building solutions rep said footings are insulated routinely by a large production builder in the Ottawa area - they have clay/silt soils that are highly prone to frost heave, and the builders insulate under the footings to protect their foundations during construction. Railway tracks are also insulated using these HI-load insulations.
More on this later.
In Europe, they are making Foamglas gravel - all with recycled glass - I think this is fantastic, but no luck getting it here.
The DOW building solutions rep said footings are insulated routinely by a large production builder in the Ottawa area - they have clay/silt soils that are highly prone to frost heave, and the builders insulate under the footings to protect their foundations during construction. Railway tracks are also insulated using these HI-load insulations.
In Europe, they are making Foamglas gravel - all with recycled glass - I think this is fantastic, but no luck getting it here.
Kitchen Recirculating Range Hoods (Ductless)
Terrel Wong of Stone's Throw Design (see link to the Rosedale House) found the VentaHood Ductless range hood on the internet - It is a nice looking unit which has 3 grease and smoke removal stages, and it doesn't use a filter pad. It employs centrifugal grease removal first, then a carbon pellet bed filter, then a large paper filter. This is the best residential ductless range hood I've seen so far. There are others by Kobe and Berbel, but this one seems the best to me, based on specs. Canadian Appliances Inc. is to give me a price on these.
Note that a large capacity ducted range hood depressurizes the house, increasing the entry of soil gases into the home - such as radon. If you are running the range hood with a fire going in the fireplace in the other room - bad situation - smoke all over the house. Also, if you are running the ducted range hood and you have a gas furnace, gas water heater - also bad situation - CO gases may easily come into the house. In these cases, you want to have a very leaky, energy hog of a house - then you might be okay.
Ductless is very much the way to go in an energy efficient, airtight house.
LT
Note that a large capacity ducted range hood depressurizes the house, increasing the entry of soil gases into the home - such as radon. If you are running the range hood with a fire going in the fireplace in the other room - bad situation - smoke all over the house. Also, if you are running the ducted range hood and you have a gas furnace, gas water heater - also bad situation - CO gases may easily come into the house. In these cases, you want to have a very leaky, energy hog of a house - then you might be okay.
Ductless is very much the way to go in an energy efficient, airtight house.
LT
Elevator
We've been working on getting an elevator on the plans for some time now - about a month or more. The idea is that we want to be able to stay put in our old age, making full use of the house. Moreover, we may be housing our aging parents in the near future, so there is need for connection from floor to floor for them. The main floor especially is sort-of barrier free for this reason. We looked at wheelchair sizes, and didn't follow barrier free requirements in the building code (it is not mandatory on this project), but worked to make as much of the building as barrier-free as possible. We also may have visitors who are in wheelchairs, or have bad knees, etc. They can enter through the at-grade side entrance, then use the elevator to access the ground floor at 3' above grade, or any other floor.
We used hoistway specs for residential elevators from the web - there are many. We intend to rough-in the shaft, and install the elevator when money allows or necessity dictates. Bob Nowak from Cambridge elevator in Cambridge, Ontario was very helpful. From him we learned that the costs of residential elevators is from $25,000 to $35,000 installed, depending on the door style. Sliding doors are more costly. The installation must be done by the manufacturer or licensed installers due to liability and warranty issues. The track comes in sections, so they are not too long to get into the house. The cab is built-up so it too is easy to install. The hydraulic cylinder is the largest item, at 1/2 the length of the required travel. In our case, the cylinder would be 15' long, 3.5" outside diameter in the body and 9" OD at the ends (for about 10") and would weigh about 400 lbs. A crane is not normally used during installation, if needed, it would cost extra. I reviewed our Revit model and figured this item can be brought in from our side entrance to the main floor, and then there is actually space to maneouver it into the shaft at the first floor area. Cambridge feels the hydraulic elevator is the safest type (there are VFD AC motor/gear styles as well - no Hyd Cyl).
The hoistway can be made with 2x4 framing or with 2x6. It needs drywall inside to achieve the fire ratings. Noise is very low due to the submersed motor (like a dishwasher, on the up cycle only - no pumping is needed on the down). I also asked what happens if the hoistway is built a little too large - Bob said Cambridge builds all the cabs custom anyway, so they grow the cab to fit the hoistway.
We also need a 90 degree type of elevator which has two doors - front and side. One can buy elevators with doors on front and back, on the front only, or front and side. We needed one of the hoistway doors to be a sliding barn door style. While the two cheaper models use swinging doors on the hoistway (and accordian or slider on the cab), Bob said the hoistway door can be made to be a slider rather than a swinging - There are interlocks on these doors so they can't be opened unless the elevator cab is there. This slider possibility allows us to access a narrow landing with the elevator where there is no space for a swinging door. This means the cheaper elevator models without automatic doors are still OK in our plan.
We will be roughing in the shaft, so each floor will have a large closet-like space. We will remove the floors in these closets when it is time to install the elevator.
LT
We used hoistway specs for residential elevators from the web - there are many. We intend to rough-in the shaft, and install the elevator when money allows or necessity dictates. Bob Nowak from Cambridge elevator in Cambridge, Ontario was very helpful. From him we learned that the costs of residential elevators is from $25,000 to $35,000 installed, depending on the door style. Sliding doors are more costly. The installation must be done by the manufacturer or licensed installers due to liability and warranty issues. The track comes in sections, so they are not too long to get into the house. The cab is built-up so it too is easy to install. The hydraulic cylinder is the largest item, at 1/2 the length of the required travel. In our case, the cylinder would be 15' long, 3.5" outside diameter in the body and 9" OD at the ends (for about 10") and would weigh about 400 lbs. A crane is not normally used during installation, if needed, it would cost extra. I reviewed our Revit model and figured this item can be brought in from our side entrance to the main floor, and then there is actually space to maneouver it into the shaft at the first floor area. Cambridge feels the hydraulic elevator is the safest type (there are VFD AC motor/gear styles as well - no Hyd Cyl).
The hoistway can be made with 2x4 framing or with 2x6. It needs drywall inside to achieve the fire ratings. Noise is very low due to the submersed motor (like a dishwasher, on the up cycle only - no pumping is needed on the down). I also asked what happens if the hoistway is built a little too large - Bob said Cambridge builds all the cabs custom anyway, so they grow the cab to fit the hoistway.
We also need a 90 degree type of elevator which has two doors - front and side. One can buy elevators with doors on front and back, on the front only, or front and side. We needed one of the hoistway doors to be a sliding barn door style. While the two cheaper models use swinging doors on the hoistway (and accordian or slider on the cab), Bob said the hoistway door can be made to be a slider rather than a swinging - There are interlocks on these doors so they can't be opened unless the elevator cab is there. This slider possibility allows us to access a narrow landing with the elevator where there is no space for a swinging door. This means the cheaper elevator models without automatic doors are still OK in our plan.
We will be roughing in the shaft, so each floor will have a large closet-like space. We will remove the floors in these closets when it is time to install the elevator.
LT
Friday, June 18, 2010
First Session of Passive House Training Completed Today
The first Passive House Training session in Canada started this past Wed June 16th 2010 and finished today. It was quite a detailed look into the Passive House Planning Package software. 24 or 25 Students attended the training and the class was full of very interesting and intelligent building professionals.
......
Will need to consider a number of changes to the house design now! Thermal mass is not as important. In-floor radiant heating is not as comforting since so little heat is transferred into the floor - there is no warm-floor effect...
......
Will need to consider a number of changes to the house design now! Thermal mass is not as important. In-floor radiant heating is not as comforting since so little heat is transferred into the floor - there is no warm-floor effect...
Monday, June 7, 2010
Grease and Smoke Removal in Kitchens
Here is quite a good intro article on grease and smoke removal, grease-fires and performance of range hoods and emerging research and technologies.
http://www.rangehoodsstore.com/articles/2010/04/grease-removal-and-kitchen-exhaust-systems/#more-5
As I read more, it seems the right way to go is to use a grease and smoke separation unit as a range hood (available for commercial kitchens - not yet found one for residential applications...), which does not exhaust air out of the building, saving what seems to be a lot of heat, eliminating the need for make-up air and the cost of all that ducting, control, shuttering, etc. There are now multiple strategies for removing grease and smoke from the stove plume - including filtering, centrifugal force, electrostatic precipitation (ionization), UV application, and some water spray technique. Apparently range hoods sometimes employ multiple strategies. Note dampers are not allowed in range hood exhaust systems, which means there would be a big hole in the house at all times if an exhausting range hood were installed- not at all acceptable.
In summer, all that waste heat from the stove stays inside the kitchen if the range hood does not exhaust the air to the outdoors. This is probably somewhat addressed by opening a window, if there is no AC system.
LT
http://www.rangehoodsstore.com/articles/2010/04/grease-removal-and-kitchen-exhaust-systems/#more-5
As I read more, it seems the right way to go is to use a grease and smoke separation unit as a range hood (available for commercial kitchens - not yet found one for residential applications...), which does not exhaust air out of the building, saving what seems to be a lot of heat, eliminating the need for make-up air and the cost of all that ducting, control, shuttering, etc. There are now multiple strategies for removing grease and smoke from the stove plume - including filtering, centrifugal force, electrostatic precipitation (ionization), UV application, and some water spray technique. Apparently range hoods sometimes employ multiple strategies. Note dampers are not allowed in range hood exhaust systems, which means there would be a big hole in the house at all times if an exhausting range hood were installed- not at all acceptable.
In summer, all that waste heat from the stove stays inside the kitchen if the range hood does not exhaust the air to the outdoors. This is probably somewhat addressed by opening a window, if there is no AC system.
LT
Kitchen Range Hood 2
Having said all I did on the Kitchen Range hood, there is another approach, which is probably better.
Here is the link:
http://www.drexel-weiss.at/?p=f3is49j-f0is1l132j-f1is27l75j-f5is3j-lng1-l75
This is a company specializing in energy and ventilation systems for Passive Houses. Basically, they are saying that a kitchen needs no special exhausting - the ventilation system will suffice. It does, however, need a range hood for the purpose of removing the fat from the stovetop fumes. they are not more explicit than that, but I think it means a range hood with grease separators, which just sends the cleaned, degreased and desmogged air back into the kitchen for the ventilation system to perform the final cleanout. What a simple (and attractive) approach! Will work to find out more about this.
LT
Here is the link:
http://www.drexel-weiss.at/?p=f3is49j-f0is1l132j-f1is27l75j-f5is3j-lng1-l75
This is a company specializing in energy and ventilation systems for Passive Houses. Basically, they are saying that a kitchen needs no special exhausting - the ventilation system will suffice. It does, however, need a range hood for the purpose of removing the fat from the stovetop fumes. they are not more explicit than that, but I think it means a range hood with grease separators, which just sends the cleaned, degreased and desmogged air back into the kitchen for the ventilation system to perform the final cleanout. What a simple (and attractive) approach! Will work to find out more about this.
LT
Earth Tube
EarthTube - A pipe in the ground exchanging heat with the soil, forming the intake for the HRV system. The soil temperatures (about 15deg C year-round) preheat the incoming winter air, improving the HRV performance quite a bit. It also cools the incoming summer air. In the summer, one would bypass the heat exchange in the HRV unit and simply bring cooled summer air from the earthtube directly into the house.
Needs to be about 8" (200mm) diameter pipe buried 6-8ft (2m) in the ground, about 150ft (45m) long, sloped toward the HRV. At the end of the slope, there will be a little well where condensate can collect and be removed. A pipe with anti-bacterial coating on the inside would be good. PH-Luft is a free online software which calculates the efficiency of the soil-to-air heat exchange, based on soil type, air flow rates, incoming air temperatures, and tube length and size, and so on. The Passive House certificate accepts the results of this software in the certification process. PH Luft is in German - bit of an issue to me, but struggling along a little bit with it.
Was told to avoid PVC for the earth tube. Of course, it has the dubious reputation of being very environmentally unfriendly both in manufacture and in use - though there are two main types of PVC, one of which has little or no plasticizer - a major factor in eco-conscious debates. The one with plasiticizer is the bad one, I think. Trouble with this is that PVC pipe is commonly available, cheap, and easy to work, creating strong, tight joins with solvent alone. Mechanically, I find it to have excellent characteristics for both the earth-tube and interior air distribution. Alas, chemically, there could be issues, though I must say, I would like to find out more about this.
The recommended material is HDPE. This stuff has to be joined by fusion-welding using a purpose-designed welding machine - I think one can see this process in Youtube videos, and its not available at the hardware store. I found Oxford Plastics makes a variety of this type of pipe, and Corix are the distributor/installer/welder, in our area. 90deg Bends and Tees, and caps area available in the larger sizes, 8" diameter, and larger still. Pipes come in straight lengths up to say 55ft (as long as a truck can take), which would make sloping the pipe in the installation easier - if you've ever worked with coiled pipe you'll know what I mean. One issue I have is that the welding process leaves a slight bead on the inside of the pipe - this will collect water and be a place for the formation of organic matter, defeating to a small degree the slope to a collection well. Of course, solvent-welded (glued) pipe will also have small grooving effects at the joints.
New Comments June 2012:
We didn't end up installing an earth tube due to costs and complexity, but also because enthusiasm for them has declined a bit.
In addition, the risks of earth tubes are not zero, though some say they are fine. Have a look a this article:
http://www.greenbuildingadvisor.com/blogs/dept/musings/belgian-passivhaus-rendered-uninhabitable-bad-indoor-air
LT
Needs to be about 8" (200mm) diameter pipe buried 6-8ft (2m) in the ground, about 150ft (45m) long, sloped toward the HRV. At the end of the slope, there will be a little well where condensate can collect and be removed. A pipe with anti-bacterial coating on the inside would be good. PH-Luft is a free online software which calculates the efficiency of the soil-to-air heat exchange, based on soil type, air flow rates, incoming air temperatures, and tube length and size, and so on. The Passive House certificate accepts the results of this software in the certification process. PH Luft is in German - bit of an issue to me, but struggling along a little bit with it.
Was told to avoid PVC for the earth tube. Of course, it has the dubious reputation of being very environmentally unfriendly both in manufacture and in use - though there are two main types of PVC, one of which has little or no plasticizer - a major factor in eco-conscious debates. The one with plasiticizer is the bad one, I think. Trouble with this is that PVC pipe is commonly available, cheap, and easy to work, creating strong, tight joins with solvent alone. Mechanically, I find it to have excellent characteristics for both the earth-tube and interior air distribution. Alas, chemically, there could be issues, though I must say, I would like to find out more about this.
The recommended material is HDPE. This stuff has to be joined by fusion-welding using a purpose-designed welding machine - I think one can see this process in Youtube videos, and its not available at the hardware store. I found Oxford Plastics makes a variety of this type of pipe, and Corix are the distributor/installer/welder, in our area. 90deg Bends and Tees, and caps area available in the larger sizes, 8" diameter, and larger still. Pipes come in straight lengths up to say 55ft (as long as a truck can take), which would make sloping the pipe in the installation easier - if you've ever worked with coiled pipe you'll know what I mean. One issue I have is that the welding process leaves a slight bead on the inside of the pipe - this will collect water and be a place for the formation of organic matter, defeating to a small degree the slope to a collection well. Of course, solvent-welded (glued) pipe will also have small grooving effects at the joints.
New Comments June 2012:
We didn't end up installing an earth tube due to costs and complexity, but also because enthusiasm for them has declined a bit.
In addition, the risks of earth tubes are not zero, though some say they are fine. Have a look a this article:
http://www.greenbuildingadvisor.com/blogs/dept/musings/belgian-passivhaus-rendered-uninhabitable-bad-indoor-air
LT
Kitchen Range Hood
Kitchen Range Hood:
The HRV system is exhausting 150 to 200 cfm of air, which has already been dried to some degree after giving up its heat to the incoming airstream. Someone has suggested using this exhaust as the make-up air for the kitchen range hood. Seems like a good idea to me. I would think one could get decent results with about 150 cfm, though some range hoods are rated 300, 400, even 600cfm. We have a Sakura range hood in our existing house (600cfm). If you need a high-performance range hood without the ridiculous high costs, the Sakura is the best we've found. For about $300, you get a dual fan, dual motor high-performance unit with turbine-style impellors and grease collection at 4 points. Four grease cups to clean, but no filter. It beats the pants off the pretty stainless units costing $1500 or more. We've had ours about 20 years without a single failure in daily use. Make sure you install it with the recommended 7" duct. We do lots of smelly cooking and frying, and I find the range hood never needs to run both fans, it is that powerful. Each fan has two speeds, and it seems running one fan at low speed is adequate for all our cooking. This could be about 150cfm. A lot of the $70 range hoods are running at 60 to 80 cfm.
A duct with a 3-way shutter could be used to redirect the HRV exhaust to the kitchen stove. In the normal position, the shutter directs HRV exhaust air out of the building. In the other position, it directs the air to the kitchen stovetop. I plan to provide a stainless long and narrow rectangular register close to stove-top height on the backsplash. Note the air temperature could possibly be a bit of a heating demand issue. Some way of equalizing the flow rate of this make-up air with the range hood exhaust flow rate is also an issue needing attention. The next challenge is the ducting needs to be valved (shuttered), and an insulated, fire-rated valve may be needed in the grease-laden exhaust terminal at the end of the kitchen range hood duct. (Otherwise air is leaking out of the kitchen range hood all the time) The insulated valve should be electronically controlled and interlocked to the range hood operation (I would think preferably with low-voltage, say 24VAC, to reduce the possibility of sparks in the grease-laden exhaust duct. A hand-operated mechanism with spring return could further reduce the chance of sparks, though I imagine operation may not be as convenient.
One more issue is that we plan to have more than one kitchen in our house. This presents another challenge, assuming the HRV flow rates are indequate for both kitchen range hoods to operate at the same time. - The best option might be to provide a dedicated 2nd earth-tube for the make-up air. another option might be to boost the HRV system flow rate with a booster fan. We've been considering a 2nd earthtube as well, though I think this is extreme - the cost of the earthtube right now seems high -see the coming earth tube article. And the 2nd earthtube would need to be placed far enough from the first to avoid a degradation in soil-to-air heat exchange.
LT
Friday, May 28, 2010
Unit cost of Insulation
How much does insulation cost?
These costs are as of about April, 2010, in the Toronto Area, in Canadian Dollars.
Note the variability in the Cellulose insulation - here is a link to one manufacturer's spec sheet.
http://www.nationalfiber.com/docs/CelPakSpecSheet1209.pdf
Fibreglass: about $0.0141 per sq ft per R1----- thickness to reach R100 (at R3.5/in) : 28.6" (726mm)
Cellulose in walls: density 3.1 lb/CF --> $.0195per SF per R1, thickness to reach R100: 28.6"
Cellulose in attics: density 1.4 lb/CF ---->$.0063per SF per R1, thickness to reach R100: 28.6"
- Based on $7/22lb bag
Ridgid XPS Foam: about $0.128 per sq ft per R1 ----thickness to reach R100: 20" (508mm)
More on this later....
These costs are as of about April, 2010, in the Toronto Area, in Canadian Dollars.
Note the variability in the Cellulose insulation - here is a link to one manufacturer's spec sheet.
http://www.nationalfiber.com/docs/CelPakSpecSheet1209.pdf
Fibreglass: about $0.0141 per sq ft per R1----- thickness to reach R100 (at R3.5/in) : 28.6" (726mm)
Cellulose in walls: density 3.1 lb/CF --> $.0195per SF per R1, thickness to reach R100: 28.6"
Cellulose in attics: density 1.4 lb/CF ---->$.0063per SF per R1, thickness to reach R100: 28.6"
- Based on $7/22lb bag
Ridgid XPS Foam: about $0.128 per sq ft per R1 ----thickness to reach R100: 20" (508mm)
More on this later....
Thursday, May 27, 2010
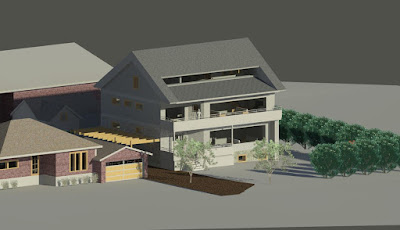
Thursday, May 6, 2010
Getting more Technical
This post will outline the energy and sustainability features for what seems to us to be good house design and Passive House Design: New ideas and information and changes to ideas will be added as time and knowledge allows - we'll elaborate on each point in future posts.
Principals of Sustainable, High-Performance Buildings as we see it:
Primary Issue: "It's the Energy, Stupid":
Research shows that the energy used by buildings over their lifetimes far outweighs any other factor related to the building's cost to the earth and environment such as embodied energy in the construction process, wastes generated, naturalness or recyclability of materials, etc. 'It's the energy, stupid' is a phrase by Joseph Lstiburek - seek him out to learn much more about building sciences - will provide a link and article on this later.
So, in short, here are the points:
- Give Priority to Low-Tech High-tech: Do the unglamorous simple things first, such as proper shape, orientation, fenestration, thermal mass, superinsulation, tight construction, and get these fundamentals right before turning to active energy systems such as PV, geothermal, etc.
- Use the PHPP software to analyze and optimize the house design. This is available from the Passive House Institute USA for $225 as of May 2010
- Maximize solar gains in winter - Careful, high-performance fenestration, building orientation. R8 Triple glazed windows with low-profile, thermally broken frames, high quality seals, and non-conductive spacers. This also means you need a clear path to sun on the south side, few or no windows on the north side, and moderate windowing on east and west. Depth of window reveals should be small on south and East sides, deep on the west side to avoid summer overheating unless there are other shade features such as trees, screens, or another building.
- Minimize solar gains in summer - fenestration, overhangs, shading and orientation. Overhangs are the main way to do this - they have the advantage of providing clear sight through the windows at all times (as opposed to sliding screens), no moving parts, and no maintenance. The disadvantage is they become part of the lot coverage - for single-storey window sizes (say 5ft tall), overhangs over south windows need to be in the range of 4ft for houses in the Toronto area. This means a sacrifice in building size, which can be a problem at times. The difference in winter to summer solar angle is 47degrees, but due to lag (the winter solstice occurs at the beginning of winter rather than in the middle) the overhangs and co-ordinated window sizes need to work with a smaller angular difference - say 30deg or so, to better block out the summer sun, and maximize gains in winter over the glass area. In Toronto, the solar angles from horizontal are 22.8deg on the winter solstice, 70deg on the summer solstice. There are many websites on line providing the values for any location on earth, including a Nasa website.
And one more thing: Absolutely no skylights, unless you can prevent heat losses through them in winter and the massive heat gains through them in summer. Here is a link to a research project in California where they built a house with no AC http://oikos.com/esb/36/Inno_Des.html - Maximize air tightness in order to allow control of energy and indoor air quality. This means very tight construction or alternative methods such as the PERSIST method, and eliminating penetrations through the thermal envelope - such as dryer exhausts, kitchen exhausts, garden hose taps, vent stacks, AC (should not be installed), etc. The dryer is something we plan to eliminate - by providing space to hang-dry clothes instead. The HRV inlets and exhausts will be through the basement floor. The vapour retarder and air barrier will be placed on th eoutside of the inner wall. The walls are a double-wall construction, of total 20" (51cm) thick, with the inside wall 2x6, then a space, then the outside walls also 2x6, so placing the vapour barrier on the outside of the inside walls will mean none of that finicky detailing so often messed up, with all manner of plumbing and wiring penetrating it. There are some issues with this approach -added cost, and how to fill it conveniently with insulation. I am leaning towards cellulose insulation. There are some excellent articles on air barriers at www.greenbuildingadvisor.com
- Maximize the efficiency of the subsequently required ventilation system - HRV, earthtube
- Maximize the effectiveness of the thermal envelope - super insulate: in the Toronto area, R60 walls, R40 to 50 basements, R80 to 120 Roof (in US imperial units) is approximately what is needed. Current minimum code requirements are R19 walls and R32 Roof, and I think R13 foundation for the top 4' of the wall only. The house in these pages is approx those higher values. Doors are especially bad energy losses- and very little in the way of high-performance doors is presently available - something like 5 or 6" thick doors provding at least R20 would help a lot. One can make the door oneself, of course - If anyone is doing this or has done this, please let me know.
- Minimize thermal bridges in all framing, windows, doors, detailing, foundations, penetrations. This, and the airtightness of the building, means careful and high-quality detailed construction using a good crew and good management, adhering tightly to the thermal-bridge-free design details. Thermal bridges can be major sources of heat loss, especially for example an aluminum threshold on an exterior door, attached to a hydronically heated concrete floor. Aluminum is to be used carefully, as its thermal conductivity is about 10 times that of steel or stainless steel. Wrapping the building in a layer of ridgid foam insulation helps a great deal. New passive houses may be designed to go beyond that by using double-wall constructions, and carefully detailed assemblies at openings.
- Minimize the surface-to-volume ratio of the building. This means bulky, cubic or spherical shapes work best. The pattern language website suggests buildings be made as 'wings of light'. Narrow, long arms stretching away from each other, so more interior spaces have access to exterior walls and therefore natural light. Two additional advantages of this approach are that the buildings can shape their outdoor spaces into various partially-enclosed spaces, and there are interior spaces in the building which are away from other spaces. The 'Wings of Light' concept has major disadvantages when it comes to energy demands. Not only is there a lot more exterior surface exposed to weather (accompanied by increased space conditioning demands), there are numerous additional detailing elements (roofs get more complex, for example), there is a major increase in floor areas lost to insulation, and the cost of construction increases (I would think significantly, due to exterior finishes and insulation).
- Maximize interior daylight, and minimize artificial lighting- this is just good house design. It seems incredible to me that so many houses being built today really don't do this. Look at any development marketed to the average home buyer, and you'll find the houses are arranged with adjacent houses directly (just 4ft perhaps) to their south. Such a house could never bring in much light, nevermind introducing solar gains. The fenestration of the houses was intended for the house to face one way, but the site planning dictates the houses are placed in any orientation that maximizes the dollar investment and use of the land. This means there are thousands of houses being built right now that could never be converted to become a passive house unless the adjacent house is removed. The other point about natural lighting is that it is much more charming than artificial lighting, and consumes no electricity.
- Minimize the lengths and number of plumbing drains and vent stacks, especially vent stacks - A vent stack can be avoided by using the air-admittance-valve (AAV), but many municipalities will not accept this as yet, I think.
- Minimize the lengths and number of hot and cold supply piping runs
- Allow windows to open so summer and shoulder season ventilation and comfort is maximized
- Take Advantage of Colours and Finishes:
The following wikipedia article is a pretty good intro to the reflectance and absorbtion issues of solar radiation.
http://en.wikipedia.org/wiki/Cool_roof - Maximize internal thermal mass - concrete seems the obvious choice, but more info is needed on materials like gypcrete and water, both of which have high heat capacities, one of which has low thermal conductivity - modelling heat flows based on day and night fluctuations in insolation, heat capacities, and thermal conductivities seems quite complex to me, though I think there are rough guidelines out there on this.
- Build for longevity, durability, permanence, fire, earthquake, flood and break & enter resistance
- Build for long-term lovability, practicality, versatility, utility
- Design for high occupancy rates, for life changes - upsizing, downsizing, barrier free, ease of reconfiguring
- Design for bicycle, scooter, walking, strollers, not just car
- Build for food security - farm, garden, greenhouse, food storage, drip irrigation, urban livestock
- Build for efficient use of space - Thin high-performance walls are better than thick, in this regard - balance with utility - make use of attic and basement space
- Build for toxin-free interiors - radon, pollution, off-gassing
- Build for moisture control and water management
Desirable and Doable Features:
We would love to incorporate all of these, but perhaps not all at once:
- Seasonal energy storage - BTES (see the Drake Landing Link)/geothermal
- Rainwater collection
- Grey water recycling
- Minimize water use, maximize water collection
- Minimize demand on city drains, electrical grid, gas supply, water supply
- Solar thermal and solar photo voltaic
- Hydronic in-floor heating-cooling
Friday, April 30, 2010

Wednesday, April 28, 2010
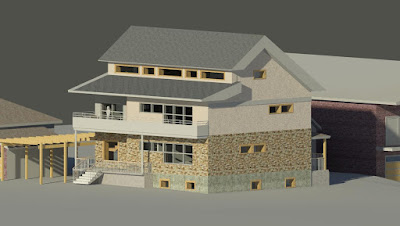
Tuesday, April 27, 2010
Exterior Design
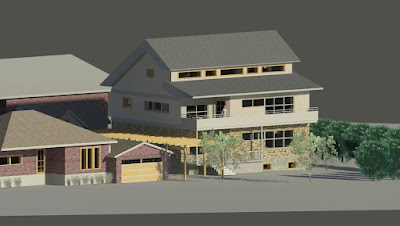
Friday, April 16, 2010
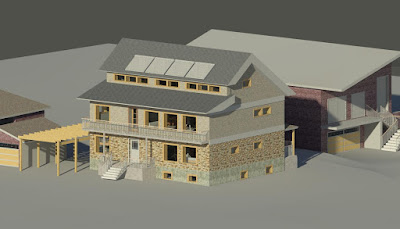
Overhangs and windows carefully arranged again. You can see we are still playing with the fenestration. The larger, curtain-wall style is nicer, I think. The windows will need to open inward, in order to avoid conflicting with the sliding screens - the balcony is very narrow anyway.
I would love to have the windows floor-to-ceiling, folding aside so the entire top floor becomes an indoor-outdoor space but alas I doubt that will be favourable to the energy demands - it would be hard to have the thermal break at the floor-to-balcony-to glass junction, not to mention the leaks and thermal bridges in all the window hinging points, - Have to look into that -
The sharp-edged roof lightens it up a bit, and achieves the needed projection without wasting vertical space. Custom, integrated gutters will be needed but are wanted since the normal gutters are really very weak and disposable, and no ladder can be placed against them - something needed to maintain those rooftop units. Somehow, these sharp edges will need to be balanced with the very thick-looking fascias on the gable ends.
The house does seem like a fatty to me. The balcony provides a constant overhang over the main floor glazing - (Balconies are not counted in lot coverage, provided they are not too large). The porch is therefore only partly covered. The front door glazing also serves to provide gain in winter, but none in summer.
Sliding screens and review of the external finishes and fenestration are going to happen soon.
Tuesday, April 13, 2010
Slit Roof with Clerestory Windows
Monday, April 12, 2010
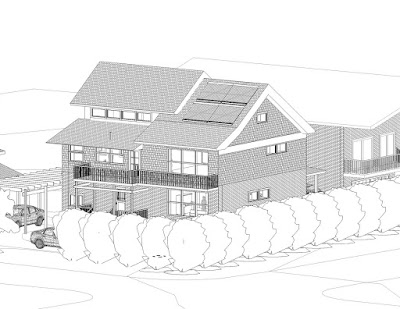
We are presently doing some deep rethinking of the design in floor plans to improve the use of the south-west floor areas and possibily reduce the number of exterior entrances from 3 to 2. Will present floor plans and other details after we get the permit. Meanwhile, experimentation with the roof has produced the following design with clerestory windows into the attic. No energy analysis has been applied to this increased exterior surface area and glass, but hopeful it will prove positive. I find the south facade too busy now, so this needs attention. One good thing energy-wise would be to remove the entrance from the south facade, as it gets in the way of the south glass. The west side would be a good place to have it - but perhaps thats too uninviting?
Monday, April 5, 2010
More experimentation with the roof. This design just below with the long balcony is the most developed with glass areas and overhangs carefully arranged to maximize solar gains in winter and shading in summer.
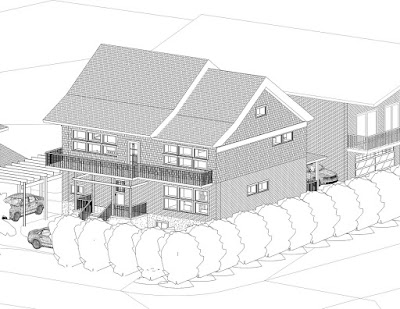
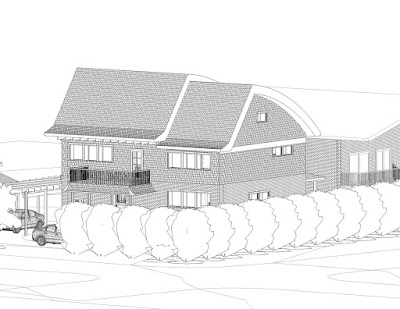
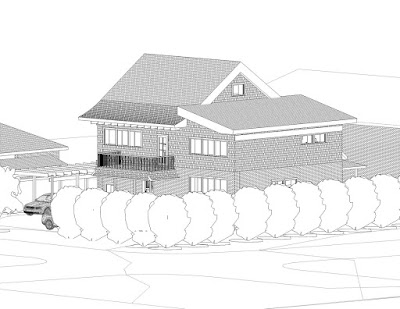
Thursday, April 1, 2010
Balcony and Curved Winglets

A balcony was requested and more whimsy on the roof so here are some more images of design experimentation. One issue with this roof is it needs to be centered on the building otherwise it looks odd. This places challenges on lot coverage due to the need for deeper overhangs on the south side. Can be resolved with projecting the east and west walls beyond the south wall.
Wednesday, March 31, 2010
North Facade
Here is a view looking south-west from the north. Note the lack of north facing windows to minimize heat losses. A major loss of heat was through the 3 entry doors on the house. To compensate, we've had to increase the R values in the roof, the foundation, and reduce the north windows. One problem I see with passive house design right now is the lack of high-performance entrance doors. They all seem too thin to me. Why not have thick vault-like (albeit not heavy) fibreglass doors with urethane foam insulation, thermal breaks, triple sealing on tapered edges and rounded corners so there is lots of insulation, continuous sealing, and heat losses and air leakage are minimized? I can't find one out there - perhaps I should look at marine applications. Would be happy to make them myself, but there is just too much to do!
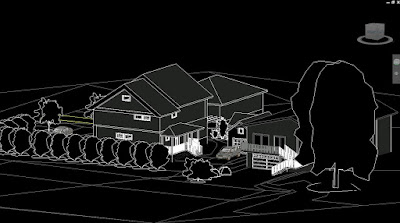
Tuesday, March 30, 2010
Recent design changes
Recent changes to the model include adjustments to sizes, locations, and number of windows on the East and South Facades. East Windows lose significant heat, and West windows introduce a lot of it, so West windows need to be minimized to reduce summer overheating and East windows kept in balance to keep heat losses down.
The neighbour's house on the north side is now included as well.
Interior layout has received a lot of changes and the stepped roof fits well with it, in addition to adding some visual interest to an otherwise vast roof. The step will also simpify the provision of conduits and 'plugs' serving solar arrays on the minor roof.
Thursday, February 25, 2010
Couple of renderings from Revit. Neighbours house on the southwest side is included. This first one is the rear, and the second one is the front again - South side.
Sun is modelled as at noon on the winter solstice, but it's probably off by about 15deg since I haven't adjusted the house orientation. The aerial view in the previous blog is aligned to true north, so you can see the streets are tilted pretty close to 15deg to the west.
LT
Aerial View
Friday, February 5, 2010
Some notes on the design:
1. We aren't architects.
2. Passive house requires volume to surface area ratios be favorable to energy conservation, so a simple, square-ish box meets the need. We had sketched a number of modern designs, but there were issues. The existing garage form is more traditional, and would have to be revised to relate to the modern design, and the height limitations are more restrictive to flat roofs (8m, instead of 8.8m to the mid-point of a sloped roof). A traditional gable is proving more spacious inside, works with the existing garage, and will relate to other houses on the street.
3. The square box is stretched in the east-west direction a little to increase the south facade, while the diminished north-south dimension means more of the light from south-facing glass (few, and very small north-facing windows are a strong need of efficient houses) will reach the back (north) side of the house.
4. The main floor is raised 3ft above grade to increase window areas to the basement, and make basement space more pleasant. This places pressure on the upper floors to keep ceiling heights modest and floor assemblies thinner. As shown, there is enough space for floors 12" thick, but just barely.
5. House dimensions are 41.5ft x 34.5ft, excluding porches, which are generally not included in lot coverage and setback calculations.
Fig 1: Site Plan
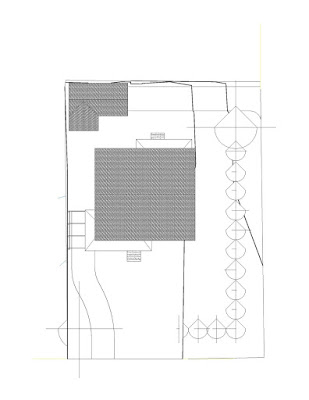
Fig 2: Viewing North-West
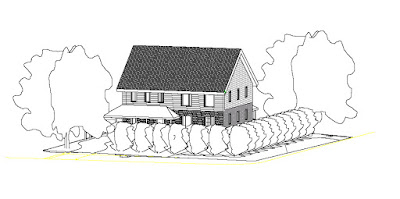
Fig 3: Viewing South-west
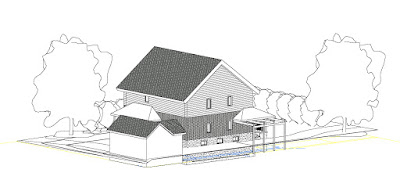
Well, here is an early version of a house design in which we've worked out a number of things, including main and 2nd floor plans, and exterior features to some degree such as windows. The exterior detailing is not really given attention yet, so there are little things to sort out. The house is tall (about 34ft or 10.5m) in this drawing, which means blending into the street-scene could be an issue, so the tall trees (12.5m oaks are shown) are intended to help in establishing context - However, the tree on the left in Fig 2 is right where a hydro-pole is, so there are issues. The curving drive is really sweet, in our minds. The lower 'shrubs' you see are 3m (12ft) tall and thick cedar hedges already existing on the site, as is the separate garage. The Revit model didn't have much available to make them look more realistic.
We intend to bury the electrical service to the house to get rid of that nasty wire running across the property.
Height is measured to the mid-point of the roof, from the crown of the road - there are two roads abutting the property in our case, so I've taken the highest point available from these.
The view shown is the south facade with the larger windows. the Passive House software was already applied to the model and there seems to be no problem with meeting the heat load and the annual energy requirements - but there is a little too much sun in summer, pushing 50% of sunny days over the 77degF comfort limit, but that is probably because I haven't entered all the shading factors as yet, not knowing the tree choices and locations.
Tuesday, January 19, 2010
Hello!
Welcome to our blog for creating a passive house in Toronto.
We look forward to engaging discussions and information about our projects and yours.
Jan. 19, 2010
We are presently in the early phases of designing and building a passive house on our residential lot in north central Toronto. A Passive house is a super-insulated and carefully designed building which uses only about 10% of the energy a normal house uses to heat and cool the interior. It is made very airtight to achieve this result, but benefits from a dedicated ventilation system (HRV or ERV), which provides excellent indoor air quality.
We look forward to engaging discussions and information about our projects and yours.
Jan. 19, 2010
We are presently in the early phases of designing and building a passive house on our residential lot in north central Toronto. A Passive house is a super-insulated and carefully designed building which uses only about 10% of the energy a normal house uses to heat and cool the interior. It is made very airtight to achieve this result, but benefits from a dedicated ventilation system (HRV or ERV), which provides excellent indoor air quality.
See www.passivehouse.us to find out more about what a passive house is.
Here are some project parameters:
The house is to have two floors and a basement. The maximum footprint of the house is 1585 sqft, due to zoning and lot coverage issues. This may include some of the eaves and porches and so forth, but at this stage, we think there are exemptions in the zoning bylaw for these features, with some conditions.
The house is to have two floors and a basement. The maximum footprint of the house is 1585 sqft, due to zoning and lot coverage issues. This may include some of the eaves and porches and so forth, but at this stage, we think there are exemptions in the zoning bylaw for these features, with some conditions.
Toronto, Ontario (North York) Lattitude 43.75deg N
Longitude 79.5deg W
Longitude 79.5deg W
Subscribe to:
Posts (Atom)